Technologia azotonawęglania w kąpielach solnych
Zestawienie najważniejszych cech i zalet naszych procesów
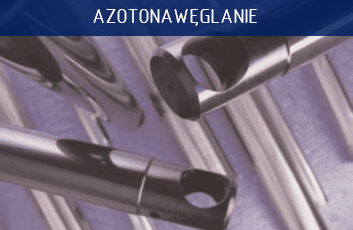
Azotonawęglanie w kąpielach solnych:
- zwiększa twardość powierzchniową,
- poprawia wytrzymałość zmęczeniową, odporność na ścieranie i zatarcie oraz właściwości antyadhezyjne,
- zwiększa odporność antykorozyjną,
- poprawia aspekty wizualne(antracytowy lub czarny kolor wyrobu).
Prowadzimy procesy azotonawęglania zgodnie z następującymi technologiami:
- ARCOR®,
- TENIFER®.
W szczególnych przypadkach w/w technologie są uzupełniane przez procesy dodatkowe.
ARCOR® (technologia firmy HEF Francja) – technologia ta składa się z poniższych procesów:
- Przygotowanie powierzchni – mycie powierzchni detali w kąpielach wodnej i alkalicznej w celu usunięcia substancji pozostałych po obróbce mechanicznej (powierzchnie zanieczyszczone olejami, emulsjami, a także środkami antykorozyjnymi) – należy poinformować zakład o rodzaju obróbki i zastosowanych środków w celu dobrania właściwej technologii mycia . Zastosowane opakowania muszą odpowiadać stanowi dostawy i być całkowicie szczelne. Zwrot towaru następuje w opakowaniach Zamawiającego w stanie jak przy dostawie.
- Azotonawęglanie (SURSULF®) – zwiększa twardość powierzchniową, nadaje właściwości trybologiczne Prowadzimy procesy w temperaturach 530 – 600oC. W przypadku detali ulepszanych cieplnie należy uwzględniać temperatury odpuszczania – proces azotonawęglania jest jednocześnie wtórnym odpuszczaniem i może prowadzić do zmniejszenia twardości warstwy zahartowanej (lub całego wyrobu). Azotonawęglanie można stosować również na warstwach uprzednio nawęglanych dla dalszego poprawienia właściwości powierzchniowych.
- Pasywacja (OXYNIT®) – zwiększa odporność antykorozyjną i nadaje atrakcyjny wygląd. Stosowany indywidualnie odpowiada wysokojakościowemu czernieniu.
- Impregnacja w środowiskach COROLAC® w różnych warunkach – stanowi trwałe zabezpieczenie antykorozyjne w trudnych warunkach eksploatacyjnych (części maszyn budowlanych, transportu szynowego, pracujących w solance i innych trudnych środowiskach chemicznych w warunkach wzmożonego tarcia).
- azotonawęglanie (TF-N® – dawniej TF-1) – zwiększa twardość powierzchniową, nadaje podwyższone właściwości trybologiczne. Stosowane jest na detalach o wymaganej niskiej chropowatości oraz małych deformacjach geometrycznych.
- mikrokuleczkowanie, dogładzanie powierzchni za pomocą mikrokulek stalowych,
- obróbka wibrościerna,
- dosuszanie w środkach ekologicznych (łupiny orzecha, ścierniwo kukurydziane itp.).
Obrabiamy stopy na bazie żelaza: stale, staliwa i żeliwa o strukturze austenitycznej lub martenzytycznej. Oferujemy szeroki wachlarz gabarytów możliwych do zaazotowania:
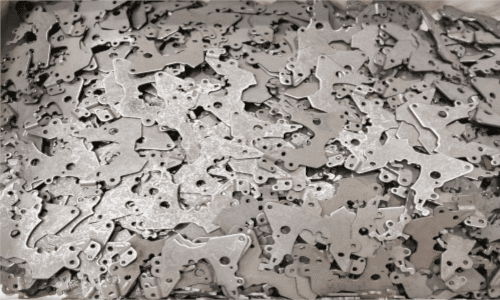
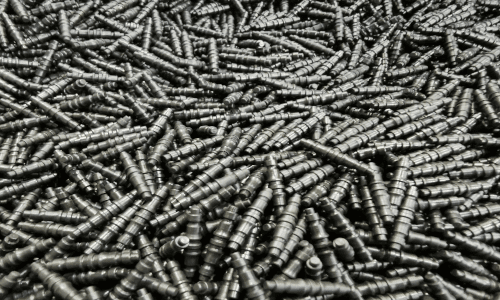
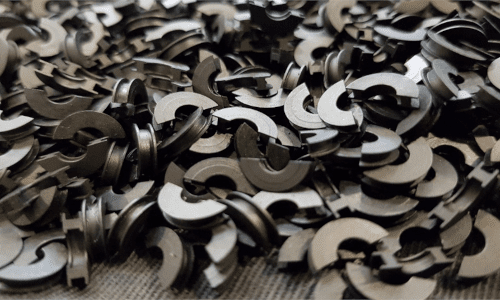
male_1
male_2
male_3
Drobne detale o wymiarze charakterystycznym 2-3 mm z wykorzystaniem specjalnie zaprojektowanych zawieszek bębnowych
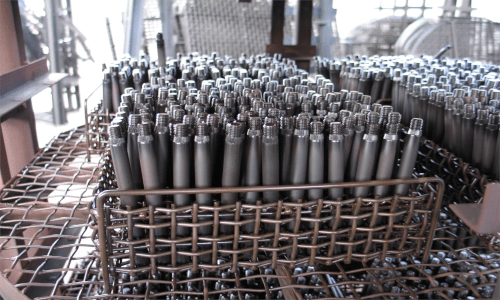
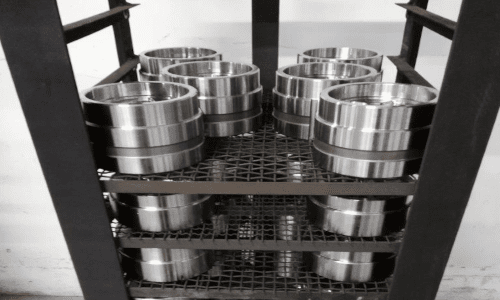
srednie_1
srednie_2
Części standardowe o gabarytach nieprzekraczających Ømax 800 mm i długości do 1800 mm dla wsadu do 600 kg masy brutto
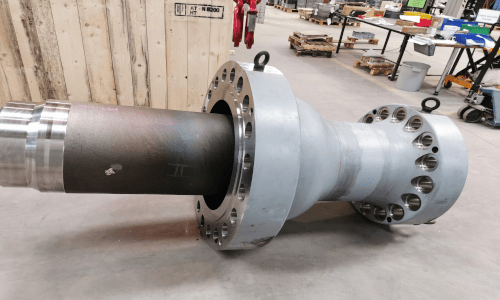
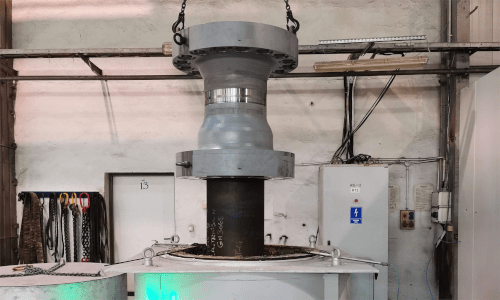
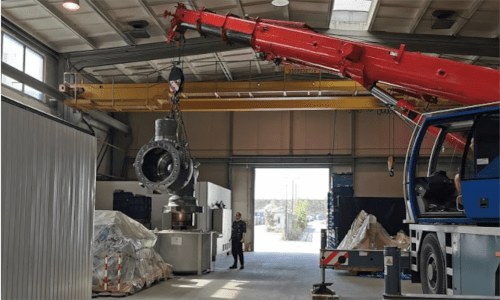
rurociag_1
rurociag_2
rurociag_3
Rurociągi, dyfuzory i inne detale o długości do 25 m i średnicy Ømax 800 mm wymagające zaazotowania fragmentu (np. końcówki)
Azotowanie w kąpielach solnych zalecane jest szczególnie na detalach:
- podlegających podwyższonemu zużyciu w warunkach tarcia,
- pracujących w trudnych warunkach środowiskowych (wilgoć, wpływ chemikaliów),
- podatnych na deformacje geometryczne podczas obróbki cieplnej wysokotemperaturowej,
- kosztownych ze względu na wykonanie ze stali wysokostopowych (możliwość zastąpienia tańszymi stalami + wykonanie procesu azotonawęglania),
- wymagających trwałych pokryć powierzchniowych (azotonawęglanie stanowi doskonałą warstwę podkładową pod inne obróbki powierzchniowe),
- wymagających trwałych warstw o stabilnej strukturze powierzchniowej (np. dla wyrobów optycznych lub trwale atrakcyjnych wizualnie),
- wymagających specjalnych właściwości towarzyszących (np. magnetycznych).
Dlatego też nasz proces jest:
- ekonomiczny,
- wielofunkcyjny,
- przyjazny dla środowiska.
Proces azotonawęglania jest ostatnim w cyklu produkcyjnym
nadającym finalne właściwości wyrobom. Dopuszczalne jest jedynie
delikatne polerowanie na tarczach korkowych lub specjalnych oraz honowanie.
nadającym finalne właściwości wyrobom. Dopuszczalne jest jedynie
delikatne polerowanie na tarczach korkowych lub specjalnych oraz honowanie.
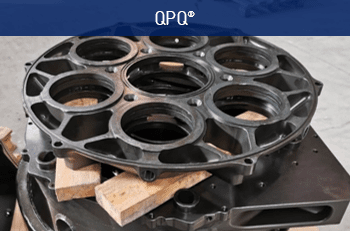
Obróbka specjalna QPQ® składa się z:
- Q – pełnego procesu azotonawęglania w technologii TENIFER® ,
- P – międzyoperacyjnego mikropolerowania powierzchni,
- Q – powtórnego skróconego azotonawęglania, pełnej pasywacji i obróbki końcowej.
Zalety w stosunku do standardowego azotonawęglania:
- podwyższona wytrzymałość zmęczeniowa,
- podwyższona odporność na zużycie przez tarcie,
- bardzo duża odporność na korozję.
Składowe procesu QPQ®:
- Q – Quenching – oznacza pełne przeprowadzenie procesu azotonawęglania i pasywacji (czernienia) oraz „zamrożenia” stanu powierzchni.
- P – Polishing – specjalistyczna obróbka mechaniczna gotowego wyrobu w celu uzyskania wysokiej jakości finalnej powierzchni o niskiej chropowatości.
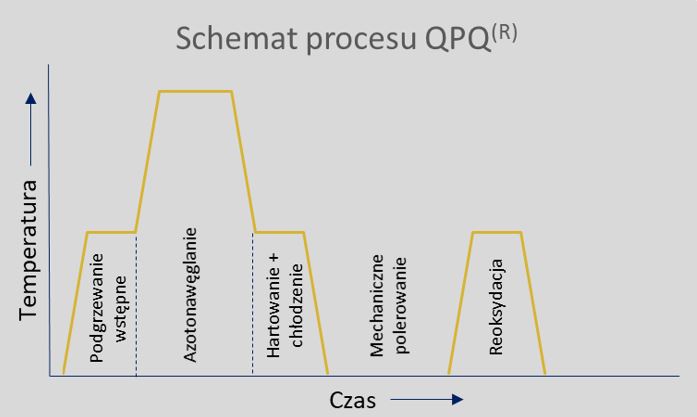
- Q – Quenching – utrwalenie oczekiwanych właściwości mechanicznych i fizykochemicznych warstwy powierzchniowej na dogładzonej powierzchni.
W procesie QPQ uzyskujemy bardzo wysokie właściwości
powierzchniowe multiplikując zalety azotonawęglania.
powierzchniowe multiplikując zalety azotonawęglania.
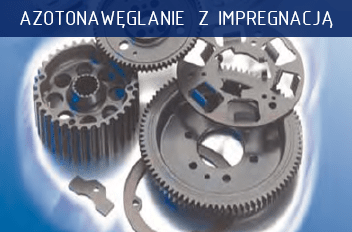
Azotonawęglanie z impregnacją COROLAC®
Proces stanowiący połączenie zalet standardowego azotonawęglania oraz impregnacji powierzchni detali. Wytworzoną specjalnie mikroporowatą warstwę powierzchniową wyrobu nasycamy trwale impregnatem zwiększając znacznie właściwości antykorozyjne. Detale po procesie odznaczają się wysoką odpornością antykorozyjną, zachowując suchą powierzchnię i nadając się
do dalszego montażu przemysłowego.