Technology of the nitrocarburizing in molten salt baths
Summary of the most important features and advantages
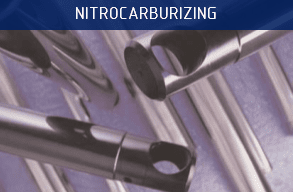
Nitrocarburizing in molten salt baths:
- increases surface hardness,
- strengthens fatigue strength, resistance to abrasion and seizure as well as anti-adhesive properties,
- enhances corrosion resistance,
- improves the visual aspects (anthracite or black product color).
We carry out nitrocarburizing processes in accordance with the following technologies:
- ARCOR®,
- TENIFER®.
In special cases, the above-mentioned technologies are supplemented by additional processes.
ARCOR®(technology from HEF France) – this technology consists of the following processes:
- Surface preparation – washing the surfaces of details in water and alkaline baths in order to remove substances remaining after mechanical treatment (surfaces contaminated with oils, emulsions, and anti-corrosion agents) – the branch should be informed about the type of treatment and the chemical substances which have been used in order to select the appropriate washing technology. The packaging must correspond to the delivery condition and be completely leakproof. The goods are returned in their Owner’s packaging in the condition as for delivery.
- Nitrocarburizing (SURSULF®) – increases surface hardness and improves tribological properties. We carry out processes at temperatures ranging between 530 – 600oC. In the case of heat-treated parts, the tempering temperatures should be taken into account – the nitrocarburizing process is also secondary tempering and may lead to a reduction in the hardness of the hardened layer (or the entire product). Nitrocarburizing can be also used on the previously carburized layers for further improvement of the surface properties.
- Passivation (OXYNIT®) – increases corrosion resistance and gives an attractive appearance. Used individually it corresponds to high-quality blackening.
- Impregnation in COROLAC® environments under various conditions – it is a permanent anti-corrosion protection in difficult operating conditions (parts of construction machinery, rail transport, working in brine and other difficult chemical environments under conditions of increased friction).
- Nitrocarburizing (TF-N® – formerly TF-1) – increases surface hardness, gives increased tribological properties. It is used on details with the required low roughness and limited and predictable geometric deformations.
- microblasting – surface polishing with micro-size cast steel shots,
- vibro-abrasive machining,
- drying in ecological agents (walnut shells, maize abrasive, etc.).
We process iron-based alloys: steels, cast steel and cast iron with austenitic or martensitic structure. We offer a wide range of sizes that can be nitrocarburized:
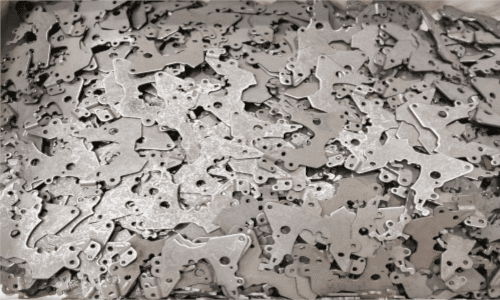
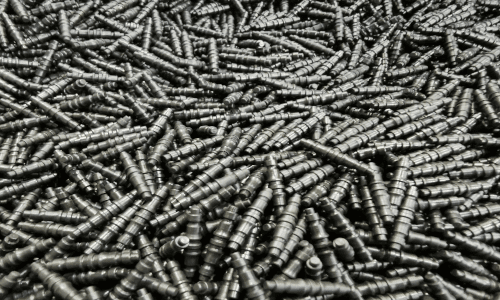
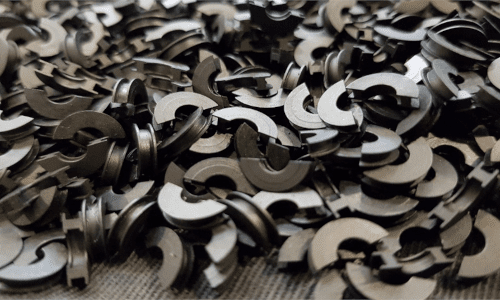
male_1
male_2
male_3
Small parts with a characteristic dimension of 2-3 mm with the use of specially designed drum jigs
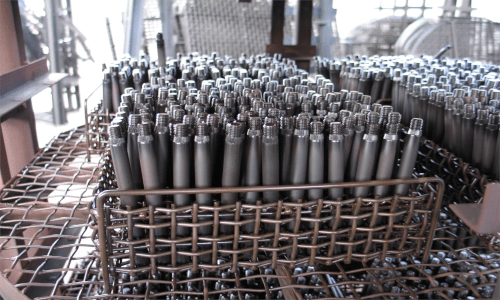
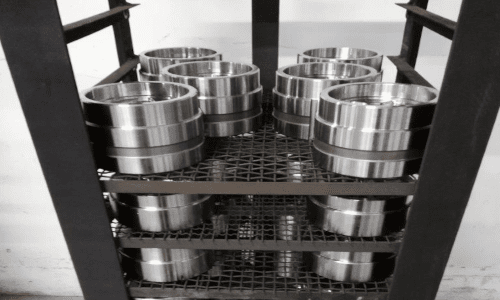
srednie_1
srednie_2
Standard parts with dimensions not exceeding Ømax 800 mm and length up to 1800 mm for a load of up to 600 kg gross weight
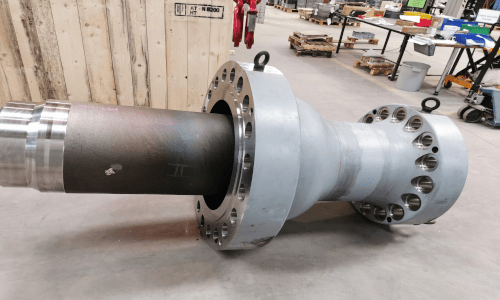
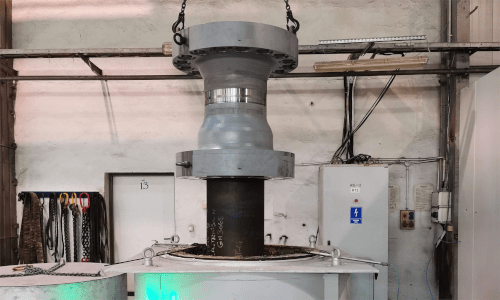
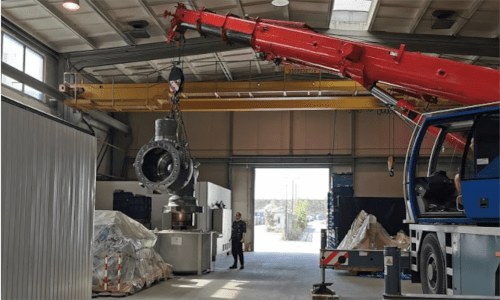
rurociag_1
rurociag_2
rurociag_3
Pipelines, diffusers and other products length up to 25 m and Ø max 800 mm in diameter requiring nitriding of a limited area
Nitriding in salt baths is especially recommended for parts which are:
- subjects to increased wear under friction conditions,
- working in harsh environmental conditions (moisture, chemicals),
- susceptible to geometric deformation during high-temperature heat treatment,
- expensive due to the fact that they are made of high-alloy steels (the possibility of replacing them with cheaper steels + carrying out the nitrocarburizing treatment),
- requiring durable surface coatings (nitrocarburization is an excellent base layer for other surface treatments),
- requiring durable layers with a stable surface structure (e.g. for optical products or permanently attractive visually),
- requiring special accompanying properties (e.g. magnetic).
Therefore our process is:
- economic,
- multifunctional,
- environmentally friendly.
The nitrocarburizing process is the last step in the production cycle and it givesthe final properties to the products. After the treatment It is only allowed to carry our fine polishing on cork or special discs and honing.
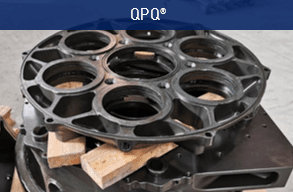
Special QPQ® treatment consists of:
- Q – full process of nitrocarburizing in the TENIFER® technology,
- P – mid-operational micropolishing of the surfaces,
- Q – shortened re-nitrocarburizing with full passivation and post-treatment.
Advantages over standard nitrocarburizing:
- increased fatigue strength,
- increased wear resistance by friction,
- very high corrosion resistance.
Components of the QPQ® process:
- Q – Quenching – means the complete process of nitrocarburizing and passivation (blackening) and “freezing” of the surface condition.
- P – Polishing – specialized mechanical treatment of the finished product in order to obtain a high-quality final surface with low roughness.

- Q – Quenching – enhancing the expected mechanical and physico-chemical properties of the surface layer on a superfinished polished surface.
We obtain very high surface properties in the QPQ®
process by multiplying the advantages of nitrocarburizing.
process by multiplying the advantages of nitrocarburizing.
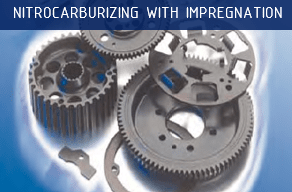
Nitrocarburizing with COROLAC® impregnation.
It is a process which combines the advantages of standard nitrocarburizing and impregnation of the surface of details. The specially created microporous surface layer of the product is permanently saturated with an impregnation agent, significantly increasing its anti-corrosion properties. Parts after the process are characterized by high anti-corrosion resistance, keeping the surface dry and suitable for further industrial assembly.