Applications for the nitrocarburizing in molten salt baths
Examples of possible applications and resulting benefits
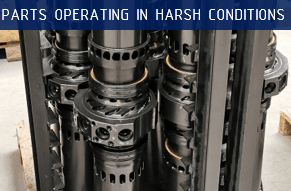
Nitrocarburizing is being applied most often to improve the surface properties of steel parts operating in harsh and demanding environmental conditions, such as:
- corrosive environment (increased humidity, salinity, chemically aggressive environment),
- difficult tribological conditions (dust, high surface load),
- high temperature.
The parts after nitrocarburizing meet the following requirements:
- low friction coefficient,
- high surface hardness,
- increased fatigue strength,
- reduced tendency to adhesion.
Bearing in mind the above, our technology is used when the following are required:
- different properties of the surface layer (strength) and core (plasticity),
- reduction of the base material costs (e.g. the use of cheaper steels after nitrocarburizing instead of expansive stainless steels),
- durable surface with further possibilities of shaping its properties.
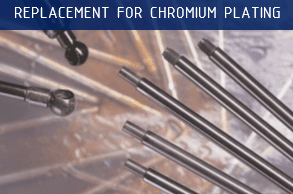
Since 2017, the use of coatings containing chromium ions Cr6+ has been prohibited in the European Union. Starting in 2025, this ban will have been strictly enforced.
Due to the mass production character of the treatment, nitrocarburizing in molten salt baths should be considered as the most serious alternative to the technology of technical chrome plating.
The benefits of hard chrome plating:
- chemical materials used in the ARCOR® and TENIFER® processes meet the REACH requirements,
- nitrocarburizing is a final step in the production chain and it does not require cumbersome mechanical finishing operations (no need to grind or polish the surface after processing),
- no risk of hydrogen embrittlement of the product,
- no exfoliation and microcracks of the surface layer – the formed layers of hard chemical compounds – nitrides of iron and other alloying elements such as chromium, molybdenum etc. as well as the nitrogen diffusion layer are not coated or applied external layers. In the cross-section of the surface layer, they constitute a smooth transition between the hardest layer in the surface area of the detail with several microns thickness to a depth of 0.2 – 0.3 mm across the material.
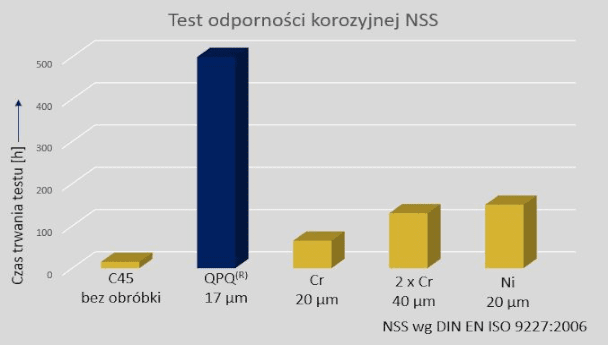
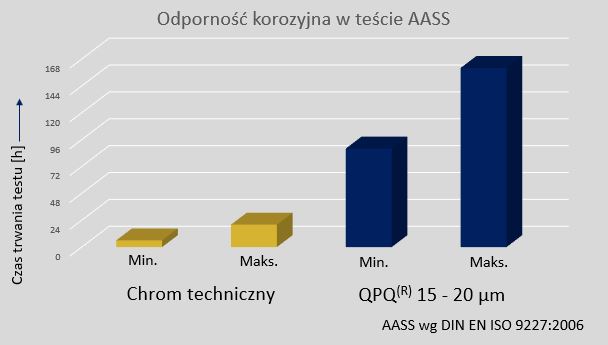
qpq_wykres_1
QPQ wykres 2
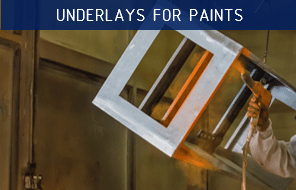
During the process of nitrocarburizing in molten salt baths we can obtain a highly developed, corrosion-resistant surface on the processed details.
It is an excellent base for applying paint coatings due to the phenomenon of increased adhesion of the coating and the surface layer of details.
Benefits of using the nitrocarburizing technology:
- permanent and durable bonding of the applied coating with the base material – the bonding layer with excellent adhesion is an integral part of the base material. It is created in a thermochemical process, it is not put on or applied,
- possibility of giving the base material additional mechanical and physico-chemical properties.

Blackening of steel (surface passivation) is the process of creating a layer of stable iron oxide on the surface of processed details. The material after the thermochemical blackening process is characterized by improved anti-corrosion properties and has a deep black color. Blackening processes are used for technical or decorative purposes.